Projects Overview C3/III AI methods for synergetic design and analysis of investigations in GRK 2250 for modelling and optimisation of impact protection systems
C3/III AI methods for synergetic design and analysis of investigations in GRK 2250 for modelling and optimisation of impact protection systems
Motivation
The methodological workflow developed in the second cohort of GRK 2250 realises a sustainable and synergetic use of research data in an interdisciplinary environment. It enables a multi-criteria optimisation of materials/structures while considering data and model inaccuracies [CON4]. The developed modelling methods show higher robustness [CON1] and performance through automated machine learning (AutoML) [CON2] and multi-task learning (MTL) [CON3] compared to the literature. Thus the potential of the workflow is proven to use existing resources more efficiently through holistic data-driven material modelling and optimisation. However, further investigations are needed to determine whether the value of the workflow can be increased by dynamically embedding the workflow in the design, execution and monitoring of the investigations and by expanding the boundaries for the synergistic use of research data.
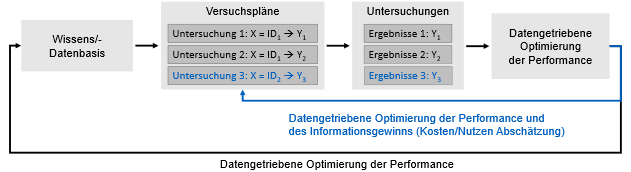
State of the art and own research
The research is founded on the workflow created in C3/II [CON1-4], which for the first time, combines the holistic data-driven modelling and optimisation of materials. Preliminary work for the synergetic use of experimental and simulation data originates from DFG-SFB 639 [IHL1, GRO1]. Approaches for the necessary further development of data management were presented in the SAB joint projects “Smart Data Services” [IHL2, IHL3] and “AMTwin” [IHL4].
Scientific questions and project goals
In C3/III, the workflow created in C3/II is to be enhanced for the optimization of materials and structures and exemplarily demonstrated for the investigations on impact protection systems. Along with this development, the following scientific questions arise. Firstly, the question needs to be answered as to how this concept can be dynamically integrated into the real and simulative test series (active learning). Currently, the optimisation of the performance of the materials/structures is a consecutive step. The aim is to ensure that the test points of the subprojects are selected dynamically concerning the maximum expected performance and the maximum information gain. Secondly, the question must be answered on how investigations with different required input features can be linked together (MTL). In this way, the material modelling can depict a broader picture of the material and the cost/information gain trade-off can be considered across investigation boundaries. Thirdly, the question should be answered as to which methods can be used to integrate simulations into the workflow. These promise a gain in information at a low cost. This way, the workflow will enable an even more efficient use of resources for the underlying investigations.
Interaction with other projects of Cohort III
For the methods of synergetic data generation and use, close cooperation with the experimental projects is required in creating and implementing the experimental design, as the experimental designs are adapted dynamically in cooperation with project C3 for maximum information gain. Likewise, the models of the numerical projects must be included depending on the defined use case. Data generation and analysis are no longer understood as two separate but parallel steps.
Literature
[IHL1] WIEMER, H., SCHWARZENBERGER, M., DIETZ, G., JUHRISCH, M., IHLENFELDT, S.: A Holistic and DoE-based Approach to Developing and Putting into Operation Complex Manufacturing Process Chains of Composite Components. Procedia CIRP 66 (2017) 147 -152. DOI: 10.1016/j.procir.2017.03.369
[IHL2] WIEMER, H., DROWATZKY, L., IHLENFELDT, S.: Data Mining Methodology for Engineering Applications (DMME) – A Holistic Extension to the CRISP-DM Model. Applied Sciences 9 (2019) 2407. DOI: 10.3390/app9122407
[IHL3] HUBER, S., WIEMER, H., SCHNEIDER, D., IHLENFELDT, S.: DMME: Data mining methodology for engineering applications – a holistic extension to the CRISP-DM model. Procedia CIRP 79 (2019) 403-408. DOI: 10.1016/j.procir.2019.02.106
[IHL4] FELDHOFF, K., WIEMER, H., IHLENFELDT, S.: FDM als Service für ein typisches Verbundprojekt in den Ingenieurwissenschaften auf Basis einer ontologie-basierten Verschlagwortung. Digital Kitchen von SaxFDM (2021). DOI: 10.5281/zenodo.5718660
[CON1] CONRAD, F., BOOS, E., MÄLZER, M., et al. Impact of Data Sampling on Performance and Robustness of Machine Learning Models in Production Engineering. Production at the Leading Edge of Technology (2023)
[CON2] CONRAD, F., MÄLZER, M., SCHWARZENBERGER, M. et al. Benchmarking AutoML forregression tasks on small tabular data in materials design. Sci Rep 12, 19350 (2022).
DOI: 10.1038/s41598-022-23327-1
[CON3] planned for 2023
[CON4] planned for 2023
Contributors
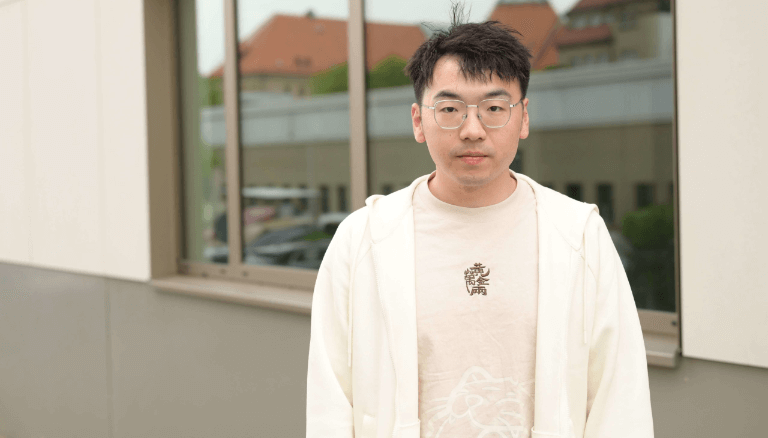
© Dominik Junger
Doctoral Researcher
DIPL.-ING. JINGHOU BI
Institute of Mechatronic Engineering
Chair of Machine Tools Development and Adaptive Controls
Technische Universität Dresden
Helmholtzstraße 7a, room E7
01069 Dresden
Germany
- jinghou.bi@tu-dresden.de
- +49 351 463 36102
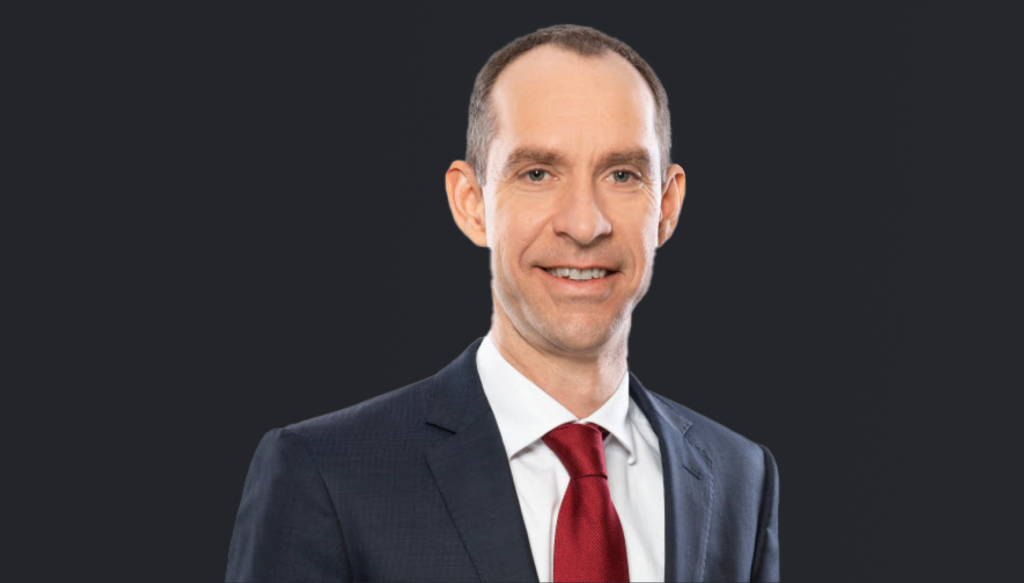
Principal Investigator
Prof. Dr.-Ing. Steffen Ihlenfeldt
Fraunhofer Institute for Machine Tools and Forming Technology IWU
Nöthnitzer Str. 44
01187 Dresden
Germany
- Steffen.Ihlenfeldt@tu-dresden.de
- Institute
- +49 351 463 34358
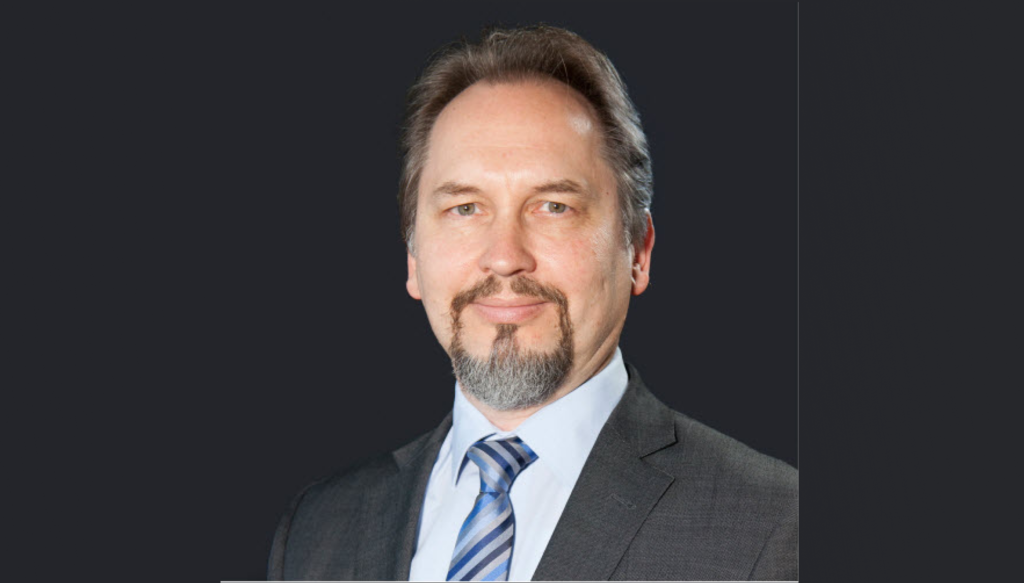
in cooperation with
Univ.-Prof. Dr.-Ing. Viktor Mechtcherine
Institute of Construction Materials
Von-Mises-Bau, 3rd Floor, Room 315A Georg-Schumann-Straße 7
01187 Dresden
Germany
- Mechtcherine@tu-dresden.de
- Institute
- +49 351 463 36311
- +49 351 463 37268
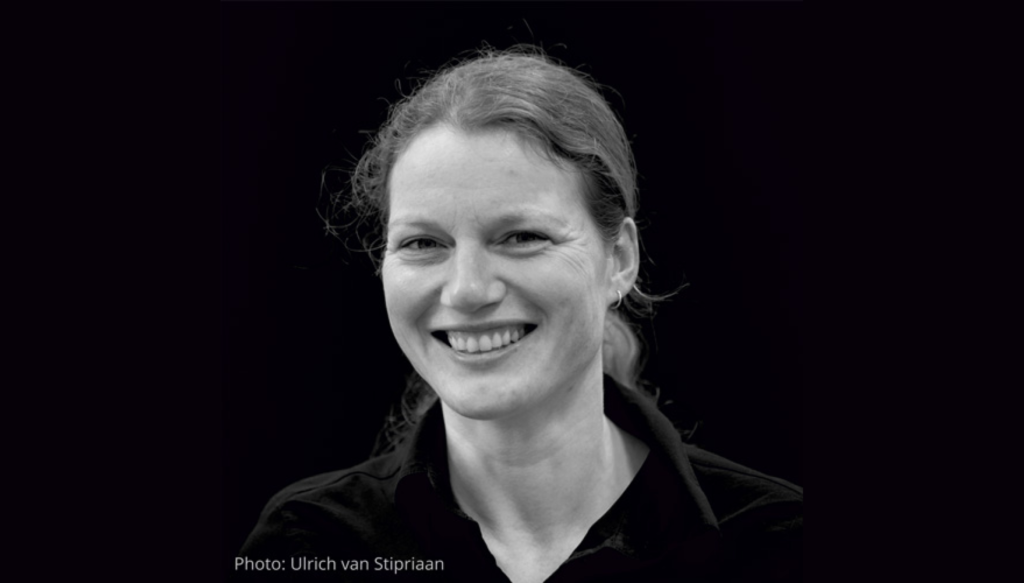
in cooperation with
apl. Prof. Birgit Beckmann
Institute of concrete structures
ABS, Floor 05, Room 027
August-Bebel-Straße 30/30A
01219 Dresden
Germany
- Birgit.Beckmann@tu-dresden.de
- Institute
- +49 351 463 38687
- +49 351 463 37289
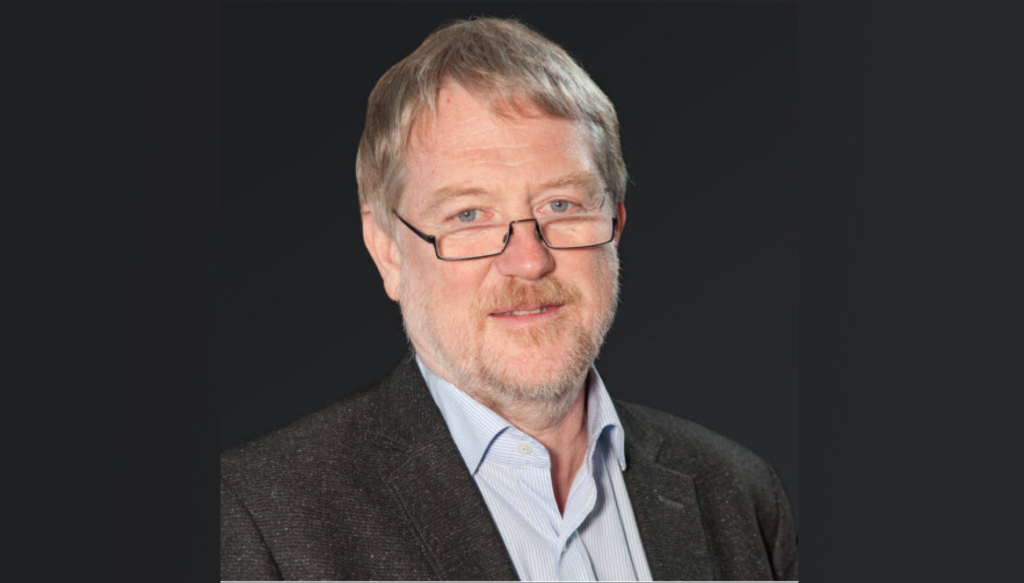
in cooperation with
Univ.-Prof. Dr.-Ing. habil. Michael Kaliske
Institute of Construction Materials
Von-Mises-Bau (VMB), Room 101A Georg-Schumann-Straße 7
01187 Dresden
Germany
- michael.kaliske@tu-dresden.de
- Institute
- +49 351 463 34386
- +49 351 463 37086