Project areas
EXPERIMENTAL: MATERIAL DEVELOPMENT
Textiles made from a variety of materials (e.g. carbon, steel, and other kinds of synthetic materials) play a crucial role in protecting concrete structures from extreme loads such as impact or blast. In particular, textiles as continuous reinforcing elements in textile reinforced concrete (TRC) can be highly effective both as protective layers on the impact side and on the rear side of concrete elements. Indeed, depending on their topology, they can withstand either severe localized shear or wide bending. In this project, the development of new textiles with 2D and 3D structures is addressed, including the possibility of making themselves diagnostic elements inside the structures, taking advantage of the electrically conductive nature of steel and carbon wires and fibers to monitor damage.
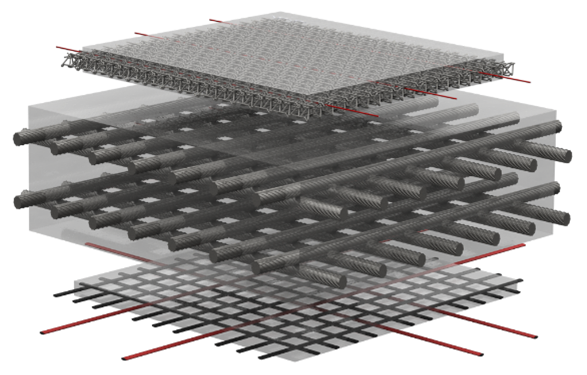
A1/Ⅱ – Gradient 3D-reinforcing structures with integrated in-situ sensors
To counteract the highly brittle nature of cementitious matrices used for strengthening purposes, the incorporation of short, dispersed fibers has been shown to provide additional toughness and ductility resources. In particular, the mechanical and physical properties of the fibers and the tailoring of the matrix/fiber interfacial bond play a major role in the overall response of the fiber-reinforced cementitious composite. In general, polymer fibers are preferred over steel fibers as far as impact loading is considered. However, poor chemical interaction with cementitious matrices impairs their ability to induce strain hardening of the composites under tensile loading. This project aims to develop novel and sustainable fibers with enhanced interfacial properties through the design of chemical and/or physical modifications.
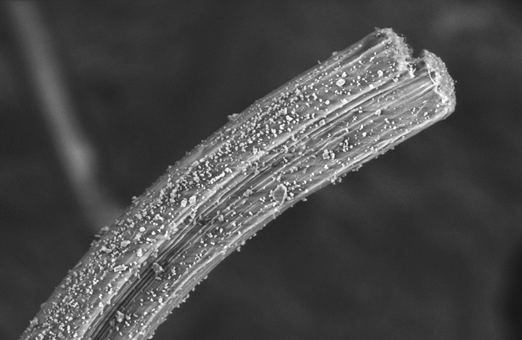
A2/Ⅰ – Strain-rate dependent composite behavior of fiber reinforcement in mineral-based matrices
A2/Ⅱ – Fiber and interphase modification for energy adsorption at high strain rates
A2/Ⅲ – Polymer fibres with chemical functionalization based on sustainable material concepts
The material design and characterization of novel hybrid composites with high ductility, i.e. strain-hardening cement-based composites (SHCC) and textile-reinforced concrete (TRC), represents the core of this project. The synergistic interaction between short, dispersed fibers and continuous textile grids imparts excellent toughness and damage tolerance to the protective layers. Spotlight is also set on the development of novel binders with a considerable reduction in the content of ordinary Portland cement to attain improved sustainability. Good candidates in this regard are alternative binders such as limestone calcined clay cement (LC3) and alkali-activated materials (AAM). In addition, the systematic investigation of the long-term performance and resistance to high and low temperatures of SHCC is of paramount importance to ensure a stable performance throughout the entire service life of the protective composite.
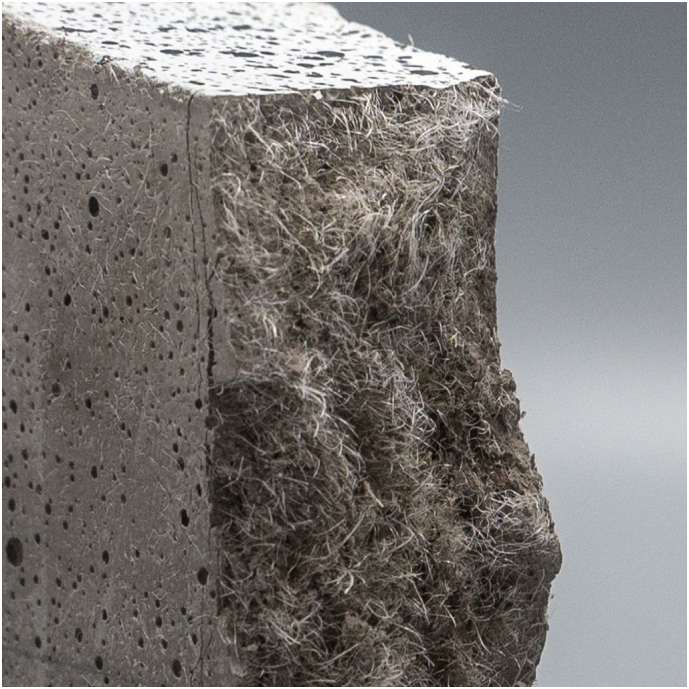
Understanding the mechanical response of complex fiber-reinforced materials is extremely challenging, due to the highly dynamic nature of the phenomena involved. In fact, while protocols for assessing the behavior of SHCC and TRC under conventional quasi-static loading regimes are widely accepted in the scientific community, there is still a limited number of studies focusing on robust testing methodologies under impact at the material scale. This project focuses on the development of new testing devices with the aim of providing a route to material characterization under tensile and shear dynamic loading. In addition, advanced automated technologies for the application of strengthening materials (i.e. shotcrete and extrusion) is addressed with the aim of improving the consistency and productivity of retrofitting operations while overcoming the issue of shortage of skilled labor.
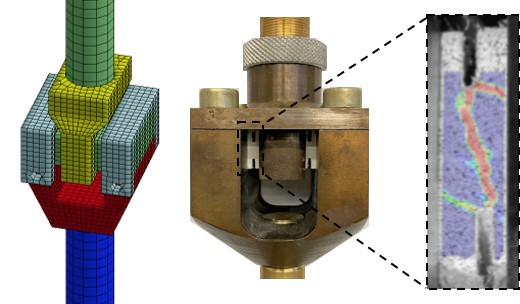
A4/Ⅱ – Characterization of the shear resistance of mineral bonded composites under impact loading
A4/Ⅲ – Fully automated reinforcement with mineral-bonded fibre composites
EXPERIMENTAL: STRUCTURAL ASSESSMENT
The complex interaction between different materials at the structural scale requires a thorough understanding from an experimental perspective, in order to envisage adequate provisions at the design stage to prevent perforation of reinforced concrete (RC) members, to increase protective effect of composite layers and ultimately to contribute significantly to human safety. On the one hand, this project deals with the experimental investigation of the behavior of RC structural elements (slabs and beams) subjected to hard impact, determining the interactions between the internal steel reinforcement and the externally-bonded composite layers in terms of damage and impact safety. On the other hand, this complex system needs to be simplified to model and describe the behavior and the mechanisms of strengthening layers for their design in construction.
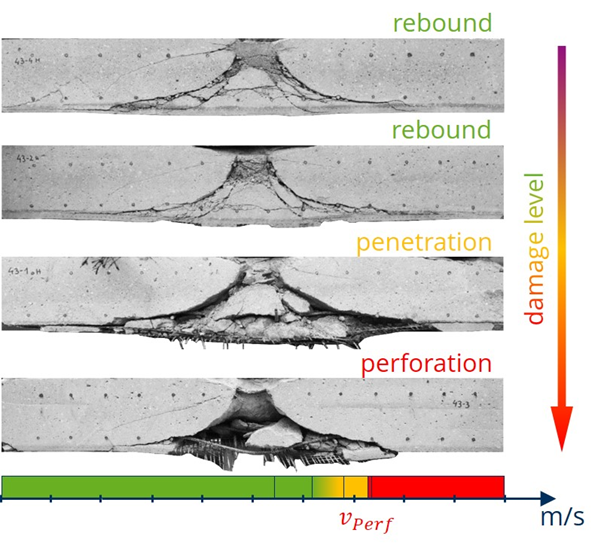
A5/Ⅰ – Strengthening of plane RC elements against impact on the impact-far side
The strengthening of reinforced concrete (RC) structures is challenging as design criteria need to move from the traditional strength-driven approach to a ductility-driven approach. While it is very important to differentiate the mechanical features of reinforcements placed on the impact side from those on the far side of the structural member, which are subjected to distinct loading scenarios, in practice a unified design is required that combines effective dissipation and strengthening actions, provided by a multifunctional layered external reinforcement. Dissipation is provided by fine-tuned lightweight materials whose damage and deformability allow for effective damping action that mitigates the input energy resulting from impact, while strengthening is provided by high performance composites. This unified design concept is also addressed in the project, with particular attention to two major engineering problems, i.e. RC slabs and compressed columns.
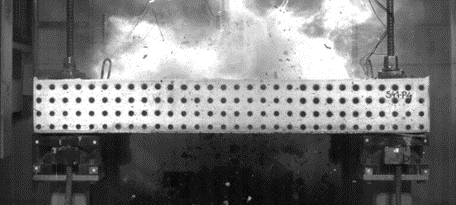
A6/Ⅰ – Strengthening of plane RC elements against impact on the impacted side
NUMERICAL SIMULATION
For an accurate assessment and prediction of the resistance of SHCC under impact loading, the dynamic fibre pull-out behavior on the microscale in combination with crack propagation properties of the heterogeneous matrix material are crucial. To complete and substantiate experimental results, advanced computational methods for the simulation of dynamic fiber pull-out and crack propagation need to be combined and embedded in a multiscale method suitable for the simulation of localization effects. These topics are addressed individually and then merged together in this project, moving from the customized development of the multiscale projection method (MPM) to a newly developed extended phase-field method (XPFM).
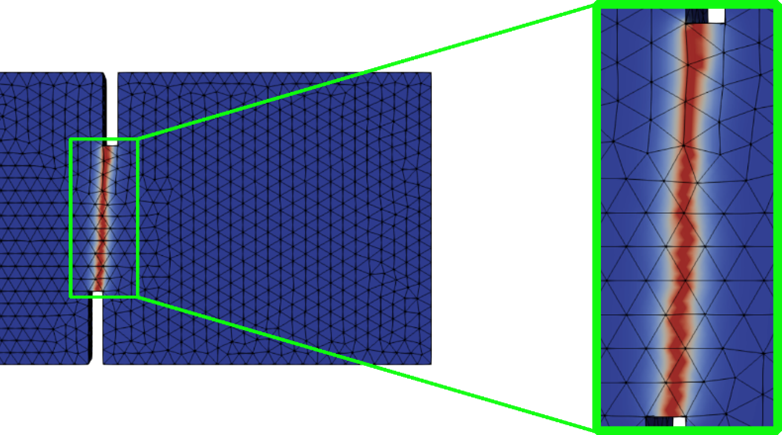
Towards a reliable simulation of the mechanical behavior of mineral-bonded complex composites, the core of this project consists in the development of a novel and advanced FEM code that allows the accurate analysis of the heterogeneous mesoscopic continuum. In this framework, aggregates or voids within a multiphase matrix can be distinguished with different discretization approaches, and the random distribution of fibers and their interaction with the matrix are also taken into account. Experimental results serve as a basis for assessing the robustness of the proposed methods and as a benchmark for sensitivity analyses based on the variation of the main parameters of the system.
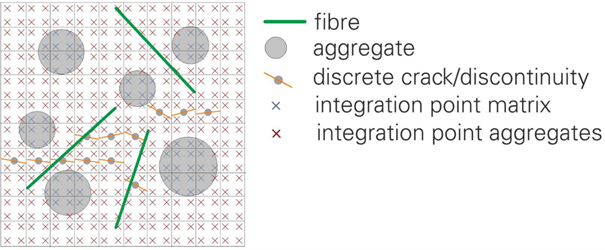
B2/Ⅰ – Modelling fiber-matrix bond and mineral-bonded composites under impact loading
Based on the material responses obtained from experimental investigations, this project deals with the fundamentals for the deterministic numerical modeling of textile and hybrid reinforced concrete at the mesoscopic level, based on the Representative Volume Element (RVE) approach. First, the development of an efficient method for the computational homogenization of the constitutive response of the material based on artificial neural networks is addressed and adapted for the application to inelastic behavior. Second, the rigorous analysis of aleatoric and epistemic uncertainties of the experimentally obtained material behavior should be considered in the numerical modeling as well as in the computational homogenization approach in order to cope with the high scatter of experimental data and obtain a realistic representation at the structural level.

B3/Ⅰ – Modeling textile reinforced components
B3/Ⅱ – Mesomechanical modelling of hybrid reinforced concrete structures at impact loading
B3/Ⅲ – Robust Design Optimization of hybrid reinforced strengthening layers at impact loading
During extreme events, structural elements subjected to impact loads are prone to severe damage due to their brittleness, e.g., object penetration and fragmentation, which dramatically increases the risks to human safety. To mitigate the risks associated with the fragmentation of structural elements, a thorough understanding of the response of structural elements is advocated, taking into account the limitations of full-scale experimental approaches. Many concurrent phenomena occur in structures during impact, such as pronounced nonlinearities, discontinuities, temperature variations, and extreme deformations. Powerful numerical tools such as the Material Point Method (MPM) coupled with finite elements (FE), Eigenfracture and Microplane Damage approaches are being developed in this project.
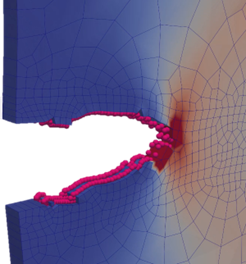
B4/Ⅰ – Simulation of the failure of reinforced concrete structures under impact
DATA-DRIVEN AND CROSS-DISCIPLINARY
In the context of impact, events occur in the time frame of few tens of microseconds. Therefore, the quantitative determination of important mechanical parameters is required to comprehensively understand the material response. Phenomena such as wave propagation, motion of fragments of structural elements and crack propagation velocity can only be monitored by sophisticated and state-of-the-art optical 3D measurement techniques, which represent a powerful tool for spatio-temporal analysis of dynamic processes in the sub-millimeter range. The aim of this project is the development and tuning of advanced techniques for the tracking of 3D deformation fields, crack analysis and the determination of trajectories and shape parameters of fragments in impact experiments as a basis for energy dissipation analyses.
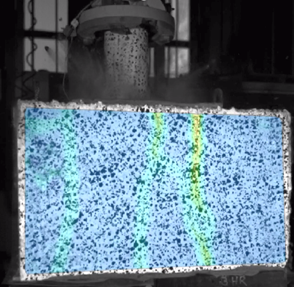
C1/Ⅰ – 3D measurement techniques of fracture processes
C1/Ⅱ – Model-based photogrammetric 3D measurements in highly dynamic processes
The development of novel materials is strongly committed to the pursuit of a more sustainable and resilient built environment, e.g. by replacing ordinary Portland cement with alternative binders from widely available natural sources, in combination with fibers with high recyclability potential. Research on the Sustainability Nexus, i.e. on the analysis of relationships, synergies and trade-offs between sustainability assessment factors, currently lacks assessment approaches for the design phase and material development in civil engineering. Missing impact categories, especially for the social dimension of sustainability, need to be developed and integrated into the assessment methods. The aim of this project is not limited to the elaboration of comprehensive sustainability parameters, but also to the integration of the resilience assessment of fibers, textiles, composites and structures.
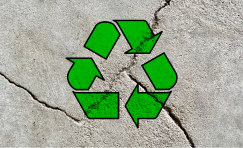
A fair, sustainable and synergetic use of research data in an interdisciplinary environment is of paramount importance to enable a multi-criteria optimization of materials/structures while taking into account data and model inaccuracies. In this context, a robust methodological approach with the use of automated machine learning (AutoML) and multi-task learning represents the main goal of this project, which ultimately aims at a more efficient use of existing resources through holistic data-driven material modeling and optimization. Within this novel workflow, second phase of the project aims at the optimization of materials and structures for the investigation of impact protection systems, drastically reducing design costs and promoting a more efficient and sustainable use of resources.
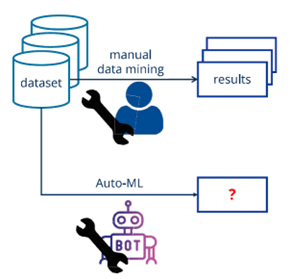
C3/Ⅱ – AI methods for the sustainable, synergetic use of the investigation results of GRK 2250 for the design and optimization of impact protection systems
C3/III – AI methods for synergetic design and analysis of investigations in GRK 2250 for modelling and optimisation of impact protection systems